Troubleshooting Viresolve? Pro Virus Filter Integrity Test Issues
Viral filtration is a common step in the production of many biologics, and viral contaminants of different particle sizes can be removed depending on the pore size of the filter. Integrity Testing (IT) is a way to confirm the retention capacity of a filter. Integrity testing before use can confirm whether the filter has been damaged during transportation and whether the filtration system is set up correctly. Post-use testing can confirm the integrity of the membrane cassette to confirm the effectiveness of the virus removal process. This article supplements the Viresolve® Pro Solution User Guide and is designed to minimize the risk of integrity test failure. Describes the key influencing factors of using automated integrity testers, troubleshooting methods and corresponding measures after test failure.
The pre-filters Viresolve® Pro Shield and Viresolve® Pro Shield H are not tested for integrity as they have no virus retention claims.
1. Integrity test of virus removal membrane package
For Viresolve® Pro virus-removing filters, which have smaller pore sizes, the diffusion flow method is typically used to test membrane package integrity. If the diffusion flow test fails, it means that the filter may not be able to meet the expected virus retention capacity, and the cause of the test failure needs to be further investigated to confirm the effectiveness of the virus removal process.
Due to membrane material compatibility reasons, Viresolve® Pro virus removal filters cannot be wetted with alcohol solutions and only have water diffusion flow indicators.
2. Precautions for using automated integrity tester
Integrity testing can be performed manually or with an automated integrity tester; for detailed testing steps, please refer to the "Viresolve® Pro User Guide". This section focuses on considerations in integrity testing.
2.1 Filter wetting
Adequate wetting is key to successful integrity testing. Before testing, the filter should be wetted with WFI at room temperature at a pressure of 2.1-4.1 bar (30-60 psi), and the wetting amount must reach 50 L/m2. After the filter is fully wetted, the water flux (NWP) can reach 131-363 LMH/bar (9-25 LMH/psi), and can remain stable for 3 consecutive measurements. If the wetting pressure is set lower than the required 2.1 bar (30 psi), a wetting volume of at least 50 L/m2 or an NWP of 131-363 LMH/bar is required. Insufficient wetting may result in integrity test failure or reduced water flux.
2.2 Connection and program editing of integrity tester
Before the integrity test, the pre-filter needs to be separated from the Viresolve® Pro filter, the liquid inlet and the downstream exhaust port (1.5 inches) are closed, the tester is connected to the upstream exhaust port (0.75 inches), and the The liquid outlet is open and connected to the atmosphere, as shown in Figure 1.
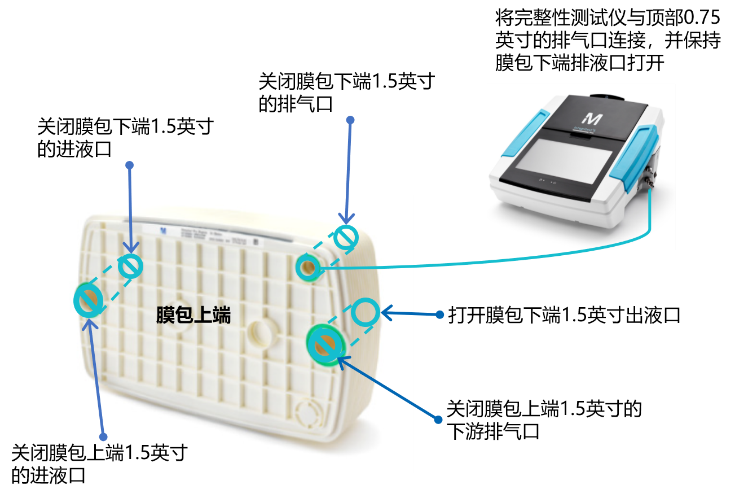
Figure 1. Schematic diagram of the connection method between the virus removal membrane package and the integrity tester.
The program settings for pre/post integrity testing are the same. After the membrane bag is wetted, check the pipeline connections, drain the excess liquid in the membrane bag, and ensure that the liquid downstream of the membrane bag has been drained before pre-pressurization. Insufficient pre-pressurization may cause diffusion flow rates to be higher than specified and result in test failure.
• (1) When using integrity tester IT4 or IT5 for pre-pressurization, the filter needs to be pressurized to 55 psi and maintained for 15 minutes; then depressurized to 0 psi and maintained for 3 minutes; and then pressurized to 5 psi, hold for 10 minutes.
(2) When using other integrity testers for pre-pressurization, the pressure can be increased to 50 psi and maintained for 30 minutes.
Most integrity testers can test single or multiple membrane cassettes simultaneously. The total diffusion flow index of multiple membrane cassettes is the sum of the diffusion flow indexes of each membrane cassette. For example, the total diffusion flow index of two Magnus 2.2 and two Magnus 2.1 membrane cassettes is ≤ 160 cc/min, that is, (2 x 60) + (2 x 20).
2.3 Analysis of reasons for failure of integrity test
If the integrity test fails, you can perform troubleshooting and retest according to the "Investigation Method for Integrity Test Failure" below. If the integrity test still fails to pass after troubleshooting, it indicates that the integrity of the membrane package may have been damaged. You can contact the default Technical support is available to assist with further investigation and confirmation.
In some tests, although the diffusion flow results met the specifications, they were outside the normal process range, and the abnormal results also required attention and investigation. Table 1 summarizes the most likely causes of virus removal package integrity failure.。
Table 1. Possible reasons for Viresolve Pro membrane cassette integrity test failure
Test diffusion flow is higher than the indicator |
|
possible reason |
improvement measures |
Insufficient filter wetting |
Confirm that the flux is within the following range: 131-363 LMH/bar (9-25 LMH/psi), rewet 50 L/m², confirm that the flux is within the range |
Wetting pressure too low (<30 psi) |
Filter flushing volume needs to be >50 L/m², or flux needs to reach 131-363 LMH/bar (9-25 LMH/psi) |
System/accessories leaking; valve not fully open/closed |
Check the status of the valve and retest; if the test fails again, replace the closed valve with a plug and retest. |
Insufficient installation pressure or gasket not fully sealed |
Confirm that the Viresolve®Pro membrane package is correctly installed on the clamp upper plate, ensure that the clamp hydraulic gauge reads 76±13.8 bar (1100 psi±200) and retest |
Damage to the membrane package (tear, poor adhesion, excessive instantaneous pressure during operation, reverse pressure damage, gasket O-ring damage) |
The filter is damaged, please contact Merck Technical Support |
Diffusion flow rate meets specifications, but exceeds typical process value range |
|
possible reason |
improvement measures |
Incorrect parameter settings of the integrity tester (insufficient pressure stabilization time); incorrect operation
|
Confirm that the parameters in the tester are entered correctly: test temperature, pressure and stabilization/pre-pressurization, then retest. |
The test indicators for multiple film packages are incorrectly set |
Recalculate the total diffusion flow index based on the number of membrane cassettes and the index of a single membrane cassette. |
Test gas/wetting fluid used incorrectly |
Retest the filter with air |
The filter outlet is clogged |
Check the installation, open the valve at the filter outlet and retest |
Flow rate lower than expected after use: membrane may be contaminated |
Check pre-filter and filter selection |
_ |
3. Investigation methods for integrity test failures
3.1 Check settings and wetting conditions
After the integrity test fails, the test parameters and operations need to be checked first. This should be done regardless of whether the air diffusion flow is close to the filter specifications. If necessary, the diffusion flow test can be performed multiple times to troubleshoot the cause. The most common cause of failure in integrity testing is incomplete filter wetting. The NWP of three consecutive measurements should be in the range of 131-363 LMH/bar (9-25 LMH/psi).
(1) For testing before use, the wetting amount must reach 50 L/m² to ensure that the NWP reaches the recommended range.
(2) For testing after use, the flushing volume needs to be greater than 50 L/m² to flush the filter, because the NWP of the filter may be lower than before use due to filter clogging.
3.2 Requirements for testing multiple film packages
If the integrity test of multiple membrane cassettes fails, you need to first check whether the membrane cassette installation and parameter settings are correct. If the second test fails, the individual membrane cassettes need to be tested to determine the root cause of the test failure. Before testing individual filters, each filter should be marked and its location recorded before retesting.
Recording pressure can help troubleshoot test failures caused by abnormal operation. If individual filters pass and are retested, tightness may be the root cause of the integrity test failure. If the retest fails, the filter supplier will need to be contacted.
Recommended Posts
-
In recent years, the hygienic condition of dental unit waterline (DUWL) has gradually received attention in China. At the same time, many local standards have been introduced. For example, Beijing issued "DB11/T 1703- 2019 Technical Specifications for Waterway Disinfection of Oral Comprehensive Treatment Units" on December 25th, 2019, while Zhejiang Province issued "DB33/T 2307-2021 Technical Specifications for Cleaning and Disinfection of Dental Waterway Systems" on January 29, 2021. In fact, various countries in the world have begun to pay attention to issues related to waterway pollution in dental treatment units much earlier, and have made relevant specifications. This article summarizes the standards of various countries in this regard as follows: Foreign standards related to the waterway of dental treatment units In 1996, the American De...
comment